Understanding Product Quality Assurance: Key Insights
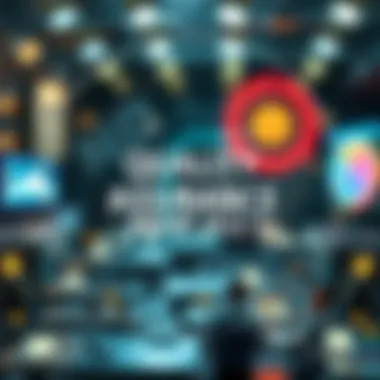
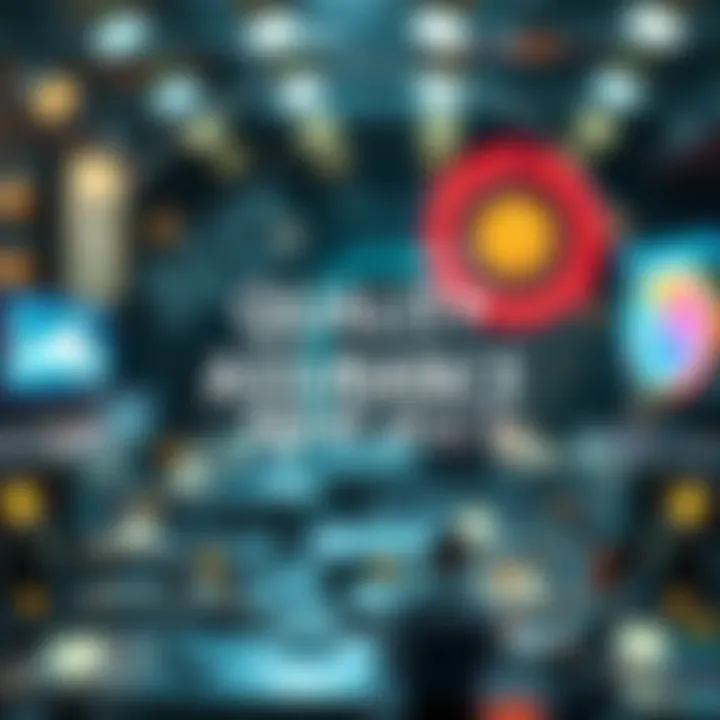
Intro
In today’s competitive landscape, ensuring the quality of products has emerged as a fundamental tenet for organizations striving for excellence. The landscape of product quality assurance (QA) is not merely about meeting regulatory standards but about establishing a robust framework that affirms a product’s integrity from inception to delivery. Engaging in quality assurance is akin to laying the groundwork for a sturdy building; without it, all that follows is built on shaky foundations.
Quality assurance encompasses a diverse spectrum of actions and methodologies designed to ensure that products perform as expected while meeting established benchmarks for quality. Overseeing this dynamic and sometimes intricate process requires keen insight and a systematic approach.
Stakeholder engagement plays a pivotal role in this arena. Various parties, including employees, suppliers, and even customers, have a vested interest in product quality. Recognizing their input and fostering a collaborative environment enhances the entire QA process, ensuring that products not only function satisfactorily but also fulfill market demands and consumer expectations. As we navigate through the essentials of quality assurance, understanding its frameworks and formulations will help demystify the complexities involved and empower individuals and organizations alike.
With the stakes high and competition fierce, mastering the art and science of product quality assurance becomes not just advantageous—it’s imperative.
Understanding Product Quality Assurance
In today’s competitive marketplace, understanding product quality assurance is not just an option; it's a necessity. It serves as a foundational pillar that ensures products consistently meet customer expectations and regulatory standards. Without a robust quality assurance system in place, businesses risk not only their reputation but also their financial health.
Clarity of Definition is crucial within this realm. Knowing precisely what qualifies as quality assurance helps teams set realistic benchmarks and performance indicators. This process benefits organizations by aligning their objectives with consumer needs and industry standards, which can enhance product reliability.
Another aspect to consider is the stronger focus on preventative measures rather than corrective actions; assessing potential weaknesses before they escalate can lead to significant long-term cost savings. Companies that take the time to analyze product development stages and external feedback systematically are better positioned to avert inefficiencies.
Furthermore, understanding product quality assurance involves a strong emphasis on stakeholder participation. When various stakeholders, from product designers to end-users, are engaged in the quality assurance process, it fosters a sense of accountability. This collective approach not only bolsters communication but ensures everyone is on the same page regarding quality standards.
"Quality is never an accident; it is always the result of intelligent effort."
In summary, comprehending product quality assurance fundamentally impacts an organization’s ability to deliver superior products while meeting or exceeding customer expectations. It forms a critical part of a company's overall strategy and can define its place within the industry.
Defining Product Quality Assurance
Defining product quality assurance involves recognizing it as a systematic approach designed to ensure that products effectively meet consistent standards throughout their lifecycle. It encompasses various processes and procedures that minimize the risks associated with production and enhances customer satisfaction.
At its core, product quality assurance is not merely about inspecting finished goods but rather integrating quality into every step of the product development process. This means active participation from the conceptual phase all the way to post-release evaluation. Understanding its intricacies is key for businesses aiming to maintain a competitive edge.
The Role of Quality Assurance in Product Development
Quality assurance plays a vital role in product development by acting as a safety net that safeguards against potential failures. It ensures that each phase of development adheres to predetermined standards, thus reducing the chances of defects emerging further down the line.
Quality assurance teams collaborate closely with product developers to embed quality-conscious practices early in the design and development phases. This tight-knit relationship assures that all team members share a unified vision of the product’s standards.
Moreover, it covers varied aspects, including:
- Testing and Validation: Regular testing validates that a product functions as intended under intended conditions.
- Documentation: Maintaining precise records provides insights into development issues and solutions, which can be invaluable for future projects.
- Feedback Mechanisms: A structured approach for gathering and acting on feedback can lead to incremental improvements and innovation in future iterations.
By emphasizing quality assurance in product development, organizations arm themselves with invaluable tools to foster creativity while mitigating risks. Thus, it becomes integral to establishing a sustainable development roadmap.
The Importance of Quality Assurance
Quality assurance (QA) is not merely a checkbox on a to-do list; it serves as the backbone of any product or service offering that aims for longevity in the marketplace. In an age where consumer expectations are at an all-time high, and the competition is fierce, effective quality assurance can mean the difference between soaring success and crashing failure. Here, we delve into the critical elements that underline its significance, along with the measurable benefits and considerations that organizations face.
Impact on Customer Satisfaction
At its core, customer satisfaction hinges on the perception of quality. When a consumer purchases a product, they expect it to function as advertised, to last, and to meet specific standards. A strong quality assurance process ensures that these expectations are not just met but consistently exceeded. This leads to:
- Increased Loyalty: Customers who experience high-quality products are more likely to return, becoming repeat buyers. The emotional connection created through reliability fosters loyalty that spans across multiple purchases.
- Positive Word-of-Mouth: Satisfied customers turn into brand advocates. They share their positive experiences with peers, adding credibility to the brand and attracting new customers.
- Reduction in Returns and Complaints: A thorough QA routine helps catch defects before products leave the facility, reducing frustrations associated with returns and complaints that plague many businesses.
In essence, investing in quality assurance directly correlates to happier customers, who, as it turns out, are vital for the bottom line.
Cost Implications of Poor Quality
On the flip side, the costs associated with poor quality can be staggering. When quality fails, it doesn't just affect the product—it ripples through various facets of the business. Understanding these implications is crucial for management and stakeholders alike. Consider the following aspects:
- Direct Costs: This encompasses recalls, warranty claims, and the expenses associated with re-manufacturing or repairing defective products.
- Loss of Reputation: A single failure can tarnish a brand's reputation, leading to a decrease in sales. Rebuilding trust takes time and resources, which could otherwise be directed towards growth initiatives.
- Operational Inefficiencies: A lack of quality assurance can lead to disruptions in production timelines and increased labor costs, as more resources may be needed to address the fallout from quality issues.
"Quality is not an act, it is a habit." – Aristotle. When organizations adopt a quality-first mindset, they protect their interests and enhance operational efficiency.
Frameworks for Quality Assurance
When navigating the intricate landscape of product quality assurance, it’s crucial to lean on established frameworks that provide structure and consistency. Frameworks for Quality Assurance are not just templates; they represent the thread that helps organizations weave quality into the very fabric of their operations. By employing these frameworks, organizations can not only uphold quality standards but also foster a culture of continuous improvement, ultimately benefitting their bottom line and elevating customer trust.
Total Quality Management (TQM)

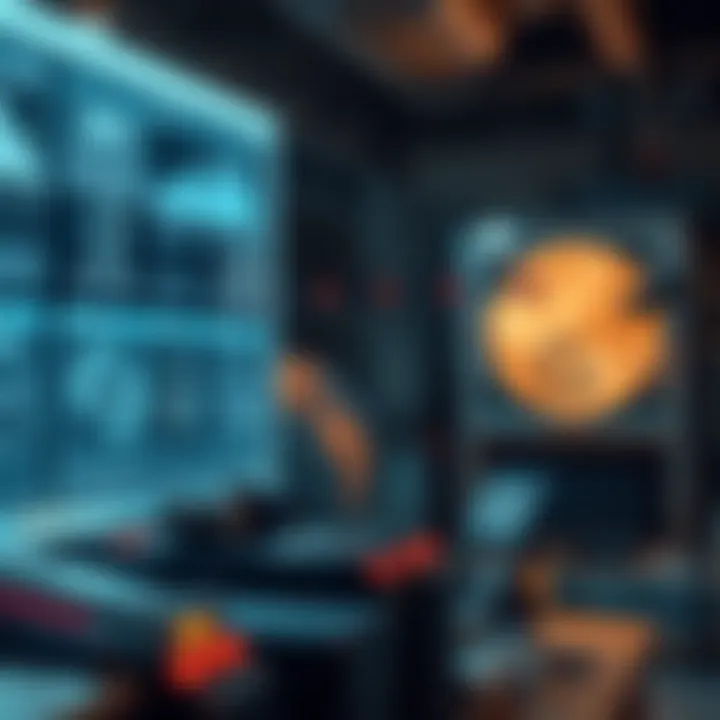
Total Quality Management, or TQM, stands as a pillar in the quest for quality excellence. TQM shifts the focus from simply inspecting products post-production to creating quality at every stage of the production process. It is a holistic approach that encompasses all members of an organization, from entry-level staff to top management.
By integrating TQM, a company can significantly enhance its operational efficiency. Key principles such as customer focus, process improvement, and team engagement are vital here. In a TQM environment, employees are not just cogs in a wheel; they are seen as essential players in ensuring product excellence. This fosters a sense of ownership and accountability.
Furthermore, TQM employs various tools such as quality circles and Plan-Do-Check-Act (PDCA), which empower teams to actively participate in problem-solving. When people are involved, the likelihood of innovation flourishes, creating a fertile ground for continuous improvement.
Six Sigma Methodology
Six Sigma is distinguished by its relentless focus on process variation and defect reduction. This methodology employs a data-driven approach to eliminate defects and improve outcomes, which is like having a skilled artisan fine-tuning a masterpiece. Central to Six Sigma are its two key components: DMAIC (Define, Measure, Analyze, Improve, Control) and DMADV (Define, Measure, Analyze, Design, Verify).
Investing in Six Sigma training can reap substantial rewards. Businesses that have integrated this methodology report reduced costs, enhanced customer satisfaction, and streamlined operations. The role of a Six Sigma Black Belt is pivotal; they lead initiatives and mentor teams in the application of these practices. This not only develops a robust foundation for quality but also equips organizations to adapt to new challenges as they arise.
ISO Standards and Certifications
ISO standards provide a universally recognized framework for quality assurance, giving organizations a competitive edge. Adhering to these standards signals to customers and stakeholders that a company is committed to maintaining high-quality processes. Certifications such as ISO 9001 are more than just badges; they indicate consistent and repeatable processes, which can lead to improved performance and reduced operational risks.
Pursuing ISO certification involves comprehensive audits and assessments, ensuring compliance with rigorous criteria. While the process may appear daunting, the long-term benefits—enhanced marketability, customer loyalty, and operational efficiency—are well worth the investment.
Ultimately, frameworks like TQM, Six Sigma, and ISO standards offer a roadmap for organizations seeking to embed quality assurance into their operations. By carefully considering these frameworks, companies can navigate challenges effectively while also ensuring that they meet and exceed customer expectations.
"Quality is not an act, it is a habit."
— Aristotle
Whether embarking on implementing TQM's holistic approach, leveraging Six Sigma's precision, or adhering to ISO's global standards, each framework provides valuable tools that can dramatically influence the success of quality assurance initiatives.
Stages of Quality Assurance
The journey of product quality assurance is multi-layered and crucial for any organization aiming to maintain high standards. Each phase not only helps in the creation of quality products but also influences the overall company image and profitability. Understanding the stages of quality assurance is essential as it allows businesses to strategize effectively, ensuring that they meet both regulatory and customer expectations. It unravels a systematic approach aimed at preventing defects, engaging stakeholders effectively, and continuously enhancing quality.
Planning for Quality Assurance
Planning is the backbone of effective quality assurance. Before diving into product development, it is imperative to lay out a blueprint for what quality means for the project at hand. This stage focuses on defining standards, establishing procedures, and identifying resources necessary to achieve the set goals.
- Setting Clear Objectives: Establishing specific, measurable goals helps in tracking quality improvements accurately. This could range from reducing defect rates by a certain percentage to ensuring customer complaints fall below a specific threshold.
- Identifying Stakeholders: Quite frankly, you can't do it alone. Engagement and input from team members, including design, engineering, marketing, and even sales, ensure that multiple perspectives shape the planning process.
- Resource Allocation: Look at it like putting together a puzzle; all pieces must fit precisely. Sufficient resources—whether it’s time, budget, or personnel—need to be allocated to bolster the quality assurance plan’s efficacy.
This stage lays a solid foundation and should never be overlooked. A robust plan often translates into fewer unexpected hurdles during implementation, enhancing overall efficiency.
Implementation and Monitoring
Implementation is where the rubber meets the road. It involves putting the quality assurance plan into action while consistently monitoring the processes in place.
- Active Monitoring: You can't improve what you don't measure. Developing key performance indicators (KPIs) that align with the objectives laid out in the planning stage is vital. Regularly reviewing these metrics keeps the team accountable.
- Training Staff: Ensuring that the entire workforce is clued in on quality standards and practices is paramount. This gets everyone on the same page and cultivates a culture of quality throughout the organization.
- Adaptation to Feedback: Feedback loops are crucial components in this stage. Encourage team members to provide input on ongoing practices and processes. Being open to suggestions ensures that necessary adjustments can be made on the fly, increasing overall effectiveness.
Evaluation and Continuous Improvement
This stage is about reflecting on your quality assurance practices, evaluating the outcomes, and finding ways to keep enhancing them continually.
- Post-Implementation Reviews: After a product launch or project completion, it’s wise to conduct a thorough review assessing whether initial objectives were met. This helps highlight successful practices and sheds light on areas needing improvement.
- Identifying Future Opportunities: Look beyond the immediate project results. Continuous improvement is not just about fixing problems; it's about striving for new heights. Investing in employee training or integrating new technologies could be avenues for enhancing quality further.
- Embarking on a Quality Culture: When an organization embraces a culture focused on continuous improvement, the results often go beyond individual projects. It fosters an environment where quality isn’t just a goal; it becomes the standard.
In summary, the stages of quality assurance are not just procedural steps but integral parts of a larger strategy that impacts customer satisfaction and operational efficiency. A solid grasp on these stages allows organizations to pivot quickly, making them agile and more capable of meeting market demands.
Tools and Techniques in Quality Assurance
In the realm of product quality assurance, having an arsenal of effective tools and techniques can spell the difference between mediocre outputs and products that shine. These tools not only help in maintaining standards but also facilitate the continuous enhancement of quality processes. It's crucial for organizations to leverage these methodologies to anticipate potential issues rather than merely react to them;
- Efficiency: These tools streamline processes, saving both time and resources.
- Data-Driven Decisions: They provide insights that aid in making informed choices regarding quality enhancements.
- Consistency: Utilizing standard procedures ensures uniformity in the quality of outputs.
- Stakeholder Confidence: Employing these tools builds trust among consumers and investors alike, reinforcing the brand's reliability.
Quality Audits
Quality audits serve as a snapshot of an organization’s commitment to quality assurance. In practice, these can be internal evaluations or external assessments by third parties. The primary objective of a quality audit is to ascertain whether the processes are being adhered to and if they align with predetermined quality standards. During an audit, auditors typically assess:
- Process Compliance: Are the established guidelines being followed effectively?
- Frequency of Issues: How often do deviations occur, and are they being remedied timely?
- Documentation: Is everything appropriately recorded for future reference?
A well-executed audit not only identifies areas of improvement but also highlights strong practices worth maintaining.
Quality audits are not merely about spotting flaws; they are about fostering a culture of accountability and proactive improvement. In many industries, a solid audit trail is also a regulatory requirement, particularly in sectors like healthcare or finance. When firms consistently engage in quality audits, they position themselves as credible players in their respective markets.
Root Cause Analysis
Root cause analysis (RCA) is a pivotal technique primarily used to identify the foundational reason behind quality failures. Without understanding the root cause, organizations might find themselves perpetually addressing symptoms without ever solving the underlying problem. The phrase 'peeling back the onion' comes to mind, as once you peel away one layer of problems, there’s likely another beneath it.

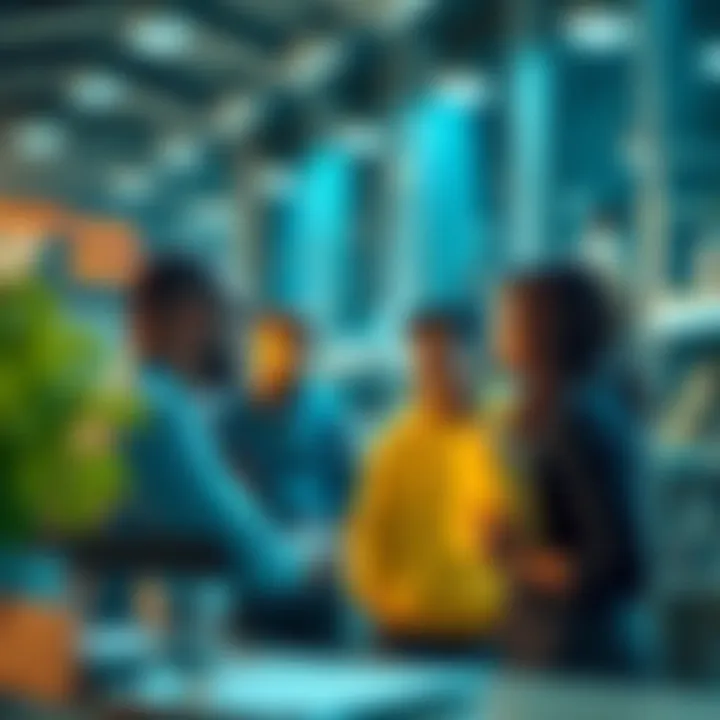
When conducting an RCA, several tools like the Fishbone diagram or the 5 Whys technique can be incredibly effective. The steps typically include:
- Identify the Problem: Clearly define what went wrong.
- Gather Data: Compile information surrounding the incident to gain a better understanding.
- Analyze the Causes: Apply RCA tools to drill down to the fundamental issue.
- Develop Solutions: Concoct ways to eliminate the root cause and prevent reoccurrence.
- Monitor Improvements: Check that the solutions are effective and sustainable over time.
RCA not only streamlines processes but also fosters a culture of learning and resilience. Adopting this technique can mean the difference between recurring issues and a genuinely resilient organization.
Statistical Process Control
Statistical process control (SPC) leverages statistical methods to monitor and control a process. This technical tool is invaluable for detecting variations that may lead to quality lapses. By plotting quality data on control charts, organizations can visualize performance over time and identify trends that warrant attention.
Key advantages of SPC include:
- Early Detection: Identifying problems before they become significant can save resources and maintain quality.
- Decision Making: Data supports decision making and reduces reliance on guesswork or assumptions.
- Continuous Improvement: SPC establishes a baseline for quality and fosters incremental improvements.
Implementation typically involves gathering data, choosing appropriate control charts, and establishing limits based on historical data. Continuous training and stakeholder involvement are crucial here; everyone from management to floor staff needs to understand the importance of data integrity in maintaining quality standards.
In essence, when organizations harness the power of statistical process control, they gain a clearer understanding of their production landscape, allowing them to ensure that quality isn’t just a target, but a consistent reality.
Quality Assurance in Various Industries
Quality assurance in various industries acts as the linchpin that holds product credibility and customer trust together. Across fields, its significance cannot be overstated; it ensures that items meet specific standards while also addressing the unique challenges and expectations inherent to each sector. The key here is to understand that quality assurance is not just a set of guidelines or processes, but rather a strategic approach that seeks to enhance and optimize product performance and reliability.
Moreover, quality assurance brings several benefits to industries, including:
- Enhanced Customer Satisfaction: By adhering to established quality standards, companies can meet or even exceed customer expectations.
- Cost Efficiency: Early detection of flaws can save companies from incurring high costs related to returns, defects, and damage to brand reputation.
- Regulatory Compliance: Many industries have stringent regulations that require products to fulfill specific quality metrics. Non-compliance can lead to legal repercussions and loss of market access.
Manufacturing Industry Standards
Manufacturing is perhaps the most recognizable sector in which quality assurance plays a critical role. Quality assurance in this industry often revolves around methodologies such as Total Quality Management (TQM) and ISO 9001 certifications. These frameworks help manufacturers to systematically oversee their processes, materials, labor, and output to minimize defects.
A few considerations in manufacturing might include:
- Continuous Improvement: Emphasizing a culture of ongoing enhancement helps in reducing waste and improving process efficiency.
- Quality Control Points: Implementing specific checkpoints during production processes can catch errors early, before products reach the market.
"In manufacturing, quality is not an act; it is a habit."
Software Quality Assurance
Software quality assurance (QA) considerably differs from traditional manufacturing but is equally vital. With the fast-paced nature of software development, incorporating systematic quality checks can mean the difference between a successful product and a dismal failure.
Key aspects of software quality assurance include:
- Automated Testing: Leveraging tools such as Selenium or JUnit to carry out repetitive tests ensures consistency and accuracy across various stages of development.
- User Acceptance Testing: Engaging end-users in the testing phase provides valuable feedback that can lead to enhanced user experiences.
Moreover, the agile methodology often adopted in software production necessitates a shift in QA strategy. Here, quality assurance is integrated into the development phase, ensuring rapid iterations while maintaining high standards.
Healthcare Quality Assurance Practices
In the healthcare sector, quality assurance takes on a uniquely pressing importance due to the direct impact on lives. Regulations set by bodies like the Joint Commission emphasize the quality of care, patient safety, and satisfaction.
Healthcare quality assurance practices include:
- Accreditation Standards: Many healthcare facilities seek accreditation to demonstrate compliance with national standards, reassuring patients of the quality of care.
- Patient Satisfaction Surveys: Regularly evaluating patient feedback allows healthcare providers to adapt services effectively, fostering trust and improving care.
Consider for instance the rigorous protocols that hospitals employ in preventing infections. These are not merely bureaucratic formalities; they are crucial strategies that safeguard the well-being of patients.
Overall, while the nuances of quality assurance vary across sectors, the foundation remains the same: a commitment to excellence, a focus on customer needs, and an unwavering drive for improvement.
The Human Factor in Quality Assurance
Quality assurance isn't just about numbers and processes; it's often said that behind every successful system, there are people bringing it to life. Understanding the human factor in quality assurance is crucial. This section delves into the interplay between individuals and quality processes, emphasizing the significance of training, development, and stakeholder engagement.
Quality assurance relies on human insights and observations. Each team member contributes to identifying flaws in products or processes, suggesting improvements, and effectively communicating these ideas. When the human element is ignored, quality initiatives can falter since machines can't always capture the nuances that a skilled individual can. For example, a factory worker noticing subtle shifts in machinery might prevent a failure that would lead to costly downtime or recalls. Thus, weaving a fabric of skilled individuals into the quality assurance process lays a solid foundation for high-quality outcomes.
Training and Development for Quality Teams
Equipping a team with the right skills and knowledge is like giving them the tools to build a sturdy house. Training and development should be ongoing processes, not just one-off events. Investing in regular training sessions allows teams to stay abreast of the latest quality assurance methodologies. In addition, it enhances both individual and team performance, ensuring that everyone is single-mindedly focused on maintaining quality standards.
Effective training should cover:
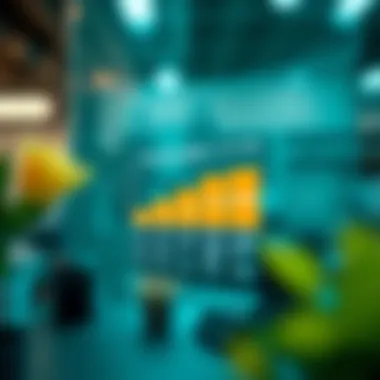
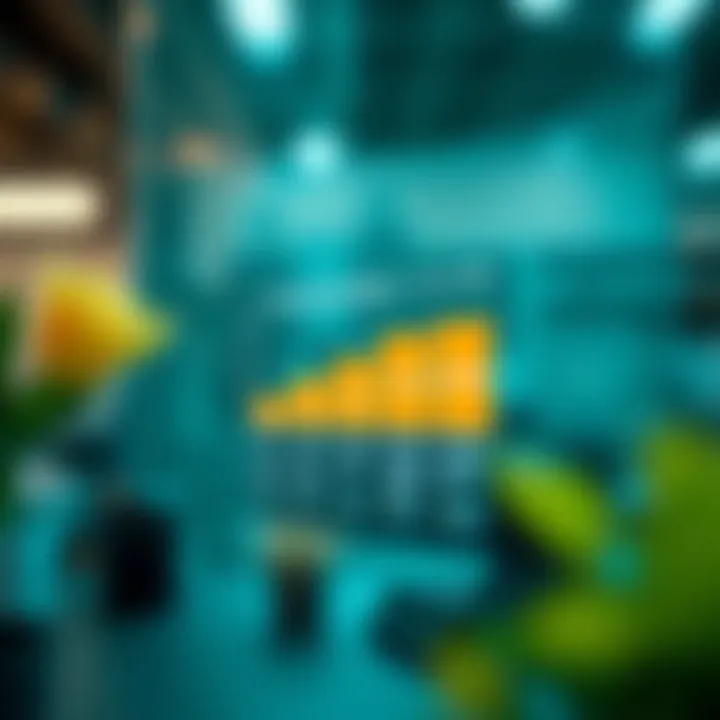
- Understanding Quality Metrics: Team members need to be well-acquainted with various quality metrics to evaluate products effectively.
- Hands-On Learning: Workshops that allow team members to practice their skills in real-world scenarios cultivate confidence and competence.
- Feedback Mechanisms: Creating a culture of feedback enables continuous improvement. When team members feel comfortable giving and receiving feedback, it fosters a solution-oriented mindset.
By prioritizing development, organizations can morph a group of people into a cohesive quality assurance team that works together toward shared goals. Moreover, companies that invest in their workforce often see reduced turnover and increased employee satisfaction, which translates into higher quality outputs.
Engaging Stakeholders in Quality Processes
To say that the quality assurance process operates in a vacuum would be an understatement. Engaging stakeholders—whether they are team members, management, or external partners—ensures that quality standards are not just set in stone, but can shift and adapt as needed according to market changes and evolving customer expectations. Stakeholder engagement creates a sense of ownership across the board.
Ways to involve stakeholders include:
- Regular Communication: Keep stakeholders in the loop about quality initiatives through consistent updates and meetings. This transparency creates a culture of trust.
- Involvement in Decision-Making: Letting stakeholders contribute to discussions regarding quality processes helps legitimize their insights and experiences.
- Gathering Feedback: Using surveys or direct conversations to solicit opinions about quality practices can unveil insights often overlooked by management.
Challenges and Barriers to Quality Assurance
Quality assurance is not just a set of procedures to ensure that a product meets certain standards; it is a critical component that can determine the success or failure of an organization. Missteps in this area can lead to significant repercussions, affecting customer satisfaction and financial outcomes. However, there are several challenges and barriers that organizations face in establishing effective quality assurance practices. Recognizing these challenges is the first step toward overcoming them.
Resistance to Change within Organizations
One of the primary hurdles in quality assurance is the deeply rooted resistance to change within many organizations. A lot of employees might be comfortable with existing processes, even if they aren’t the most efficient. Change can be seen as a threat, turning the workplace atmosphere sour. It is common to here, "But we've always done it this way!"
Some employees might worry that new quality protocols could lead to increased scrutiny of their work, even doubting their abilities. Therefore, fostering an environment that values transparency and open communication is crucial. This involves educating staff on the importance of quality assurance and the benefits of adapting to new methods. Regular training sessions and workshops can help alleviate fears while highlighting that the ultimate goal is to elevate product quality, which should benefit everyone in the long run.
"Change is the only constant in life; organizations must cultivate a culture that embraces it rather than fights it."
Moreover, involving employees in the decision-making process tends to lessen their resistance. Gaining their insight can lead to better solutions and a shared sense of ownership in quality assurance practices.
Resource Limitations and Budget Constraints
Another significant barrier to effective quality assurance is resource limitations. Organizations may often find themselves stretched thin, juggling multiple projects with limited time and manpower. Quality assurance initiatives, such as implementing new software or hiring specialized personnel, might be pushed aside due to budget constraints, with leaders believing that such investments might not yield immediate returns.
In industries where profit margins are tight, companies tend to overlook the long-term benefits of robust quality assurance practices. Instead, the focus shifts to short-term savings, ultimately leading to higher costs down the line due to defects or customer complaints.
Key strategies to overcome these resource limitations include:
- Prioritization: Identify the most critical areas in need of attention, allowing organizations to allocate resources where they matter most.
- Staged Implementation: Instead of a complete overhaul, consider a phased approach to introduce quality assurance methods. By piloting small initiatives, one can demonstrate their effectiveness and gain support for larger, more comprehensive programs.
- Leveraging Technology: Utilizing software solutions can often provide a high return on investment by automating routine tasks, freeing up resources for more strategic quality initiatives.
By understanding and addressing these challenges proactively, organizations not only enhance their quality assurance practices but also drive overall business success. Engaging stakeholders, empowering employees, and allocating resources wisely form the bedrock of a well-rounded quality assurance strategy. This leads to a more resilient organization capable of maintaining high product standards even amidst internal and external pressures.
Future Trends in Product Quality Assurance
As we delve into the ever-evolving landscape of product quality assurance, understanding future trends becomes vital for organizations aiming to maintain their competitive edge. With emerging technologies reshaping industry norms and increasing awareness surrounding sustainability, these trends play a significant role in determining how quality assurance strategies are formulated. Knowing what lies ahead not only prepares companies for inevitable changes but also helps in aligning quality assurance processes to meet new demands in efficiency and ethical considerations.
Technological Advancements and Quality Assurance
In today's digital age, technology is a double-edged sword. On one hand, it brings about complexities in quality assurance; on the other, it offers innovative solutions to longstanding problems. Machine learning and artificial intelligence, for instance, are paving the way for predictive analytics in quality assurance. Such technologies allow companies to identify potential quality issues before they occur. Real-time data can trigger alerts that enable proactive measures, thus minimizing wasted resources and enhancing customer satisfaction.
- Some notable advancements include:
- Automated Testing Tools: These tools help standardize quality checks, making it easier to ensure consistency across products.
- Data Analytics: By leveraging big data, firms can analyze past failures to formulate better quality checks for future production cycles.
- IoT in Quality Control: Internet of Things devices allow for remote monitoring and data collection, ensuring that manufacturing processes maintain set quality standards.
Adjusting quality assurance strategies to incorporate these technological advancements not only improves operational efficiency but also enhances the overall customer experience. As organizations embrace automation and digitization, they will find that their teams can focus more on strategic aspects rather than mundane tasks.
"The integration of advanced technology into quality assurance is no longer a luxury; it's a necessity for survival in a competitive market."
Sustainable Practices in Quality Management
Sustainability isn't merely a buzzword; it's becoming a foundational element in quality assurance practices across industries. Customers are shifting their preferences toward eco-friendly products, thereby prompting organizations to re-evaluate their supply chains and processes. Implementing sustainability practices in quality management isn't just good for the planet; it also enhances brand image and consumer trust.
Key considerations include:
- Life Cycle Assessment (LCA): This approach evaluates the environmental impact of a product from production to disposal, allowing businesses to identify areas for improvement.
- Sustainable Sourcing: Companies are now looking at the origins of their raw materials to ensure they are sustainably sourced and ethically traded.
- Circular Economy Models: Instead of a linear approach, businesses are exploring ways to make products last longer and be more easily recyclable, which can dramatically reduce waste.
Integrating sustainable practices into quality management implies long-term benefits, such as increased efficiency, reduced costs through better resource management, and gaining a reputation as a responsible brand. All these factors not only attract a growing demographic of eco-conscious consumers but also set the stage for innovation driven by sustainability principles.
Finale
In the realm of product quality assurance, the conclusion is not merely an end; rather, it represents a critical synthesis of the concepts and practices discussed throughout the article. Quality assurance serves as a linchpin that tightly binds customer satisfaction, operational efficiency, and financial success. It's imperative for both organizations and consumers to understand that quality is a continuous journey, not a destination.
The Ongoing Importance of Quality Assurance
Every stakeholder engaged in the production and delivery of goods recognizes that quality assurance is an indispensable aspect of business operations. Without it, risks multiply: dissatisfied customers, increased returns, and reputational damage become integral challenges. However, integrating a robust quality assurance framework offers multiple advantages:
- Enhanced Customer Trust: Customers frequently gravitate towards brands that demonstrate a consistent commitment to quality. This trust fosters loyalty, encouraging repeat purchases and positive word-of-mouth marketing.
- Cost-Effectiveness: Investing in quality assurance can lead to substantial long-term savings. Detecting defects during production is significantly cheaper than addressing issues after they reach the consumer.
- Market Competitiveness: Companies that prioritize quality assurance can differentiate themselves in saturated markets. By highlighting the integrity of their products, they can carve out a unique niche.
"Quality is not an act, it is a habit." - Aristotle
It is also essential to consider that quality assurance is not static. It adapts as market demands evolve and technologies advance. Companies need to be nimble, regularly reviewing and updating their quality processes to align with industry standards and customer expectations. Thus, moving forward, it’s apparent that product quality assurance remains a pivotal practice that will continue to influence how organizations operate and succeed in an increasingly competitive landscape.